AI Product Development
Predictive Maintenance Solution for Manufacturing Company
Client: Global Manufacturing Inc.
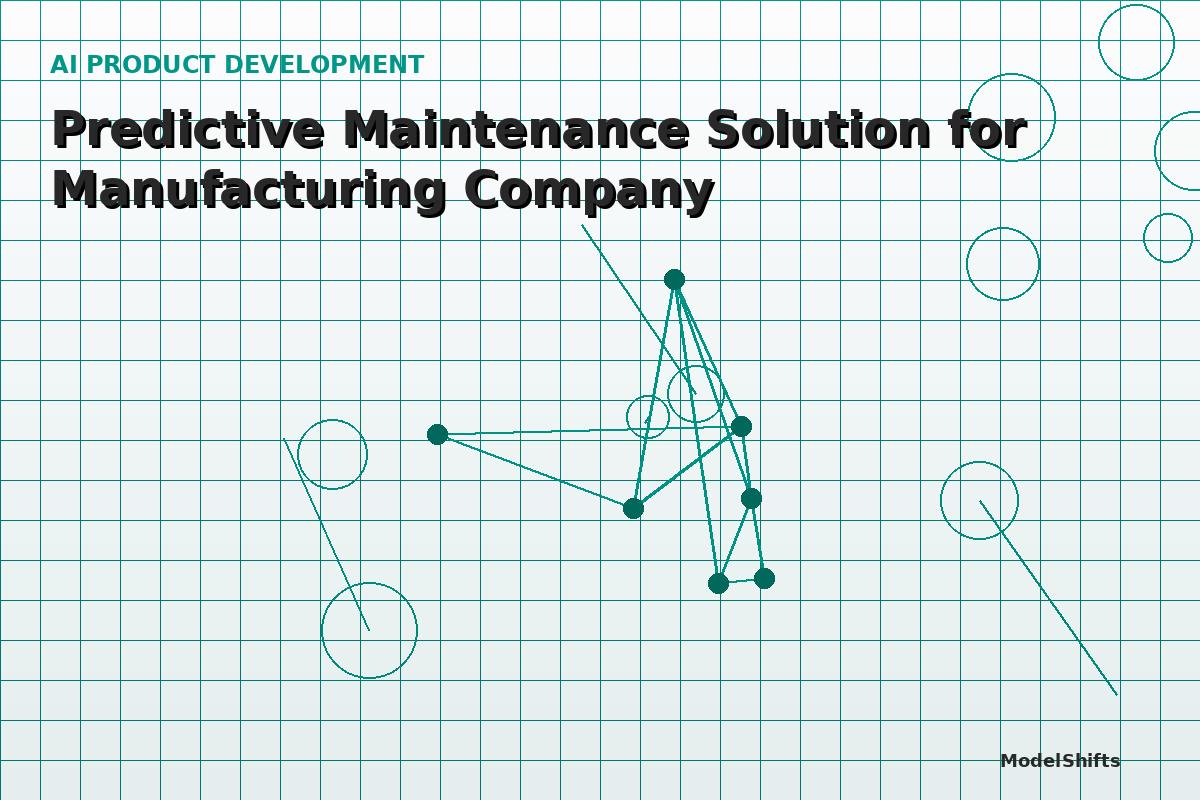
Executive Summary
Developed a custom machine learning model that predicts equipment failures, reducing downtime by 35% and maintenance costs by 25%.
Challenge
Global Manufacturing Inc., a leading player in the automotive parts industry, faced significant operational challenges due to unscheduled equipment downtime. Traditional preventive maintenance schedules were often inefficient, leading to either premature parts replacement or unexpected failures that halted production lines. This resulted in substantial financial losses from lost production hours, emergency repair costs, and compromised delivery schedules.
Solution
ModelShifts was engaged to develop an AI-powered predictive maintenance solution. Our approach involved:
- Data Integration & Preparation: We collected and integrated historical sensor data (temperature, vibration, pressure, etc.) from critical machinery, along with maintenance logs and failure records. This data was cleaned, preprocessed, and structured for model training.
- Custom Machine Learning Model Development: Leveraging advanced machine learning algorithms, including LSTMs (Long Short-Term Memory networks) and Random Forests, we developed a model capable of identifying subtle patterns indicative of impending equipment failure.
- IoT Integration: The model was integrated with the client’s existing IoT infrastructure, allowing for real-time data ingestion and analysis from machinery sensors.
- Dashboard & Alerting System: A user-friendly dashboard was created to visualize equipment health scores, predict failure probabilities, and provide actionable insights to the maintenance team. An alerting system was implemented to notify staff of critical anomalies and upcoming maintenance needs.
Results
The implementation of the predictive maintenance solution yielded significant improvements:
- Reduced Unplanned Downtime by 35%: By predicting failures before they occurred, Global Manufacturing Inc. could schedule maintenance proactively during planned shutdowns.
- Lowered Maintenance Costs by 25%: Optimized maintenance schedules and reduced emergency repairs led to considerable cost savings.
- Increased Equipment Lifespan: Proactive maintenance helped in extending the operational life of critical machinery.
- Improved Production Efficiency: More reliable equipment operation led to smoother production workflows and increased output.
Client Testimonial
“ModelShifts’ predictive maintenance solution has revolutionized our manufacturing operations. The ability to foresee potential equipment failures has not only saved us significant costs but also improved our overall production reliability. Their expertise in AI and understanding of our industry challenges were key to this project’s success.” - VP of Operations, Global Manufacturing Inc.